Zum Vorbild:
Um dem wachsenden Großstadtverkehr Rechnung zu tragen, wurden von der Großen Berliner Straßenbahn sehr früh auch vierachsige Fahrzeuge beschafft. Es begann 1898 mit dem Typ "Brandenburg".
Um größere und stärkere Motoren einbauen zu können, fand das in den USA entwickelte Maximum-Prinzip bei der GBS großes Interesse.
Die Konstruktion der Drehgestelle mit einem großen Treib- und kleinem Laufradsatz ermöglichte einen größeren Bauraum für die Motoren.
1901 erschienen die ersten Maximum-Triebwagen auf Berliner Gleisen. 1907 erschien dann der 10-fenstrige "Maximum 30" der Großen Berliner Straßenbahn im Stadtbild.
Der Triebwagen 2990 ist in diesem Zustand heute als Museumswagen betriebsfähig erhalten.
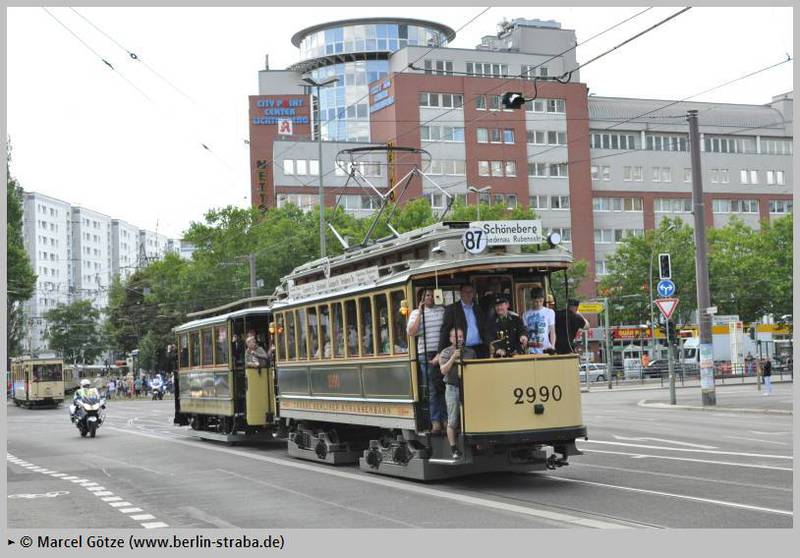
1925 begann der Umbau der offenen Wagen auf geschlossene Plattformen und elektrische Bremse.
Fortan wurden diese Wagen als TD 07/25 bezeichnet. Tw 5256 ist in diesem Zustand als historischer Wagen im Bestand der Berliner Verkehrsbetriebe.

Nach der Teilung der Verwaltung der BVG begann die BVG-Ost ab 1951, die Wagen grundlegend umzubauen. Dies geschah bei mehreren Firmen. Unter Anderem erhielten die Wagen ein Tonnendach und seitliche Lüftungsklappen über den Seitenfenstern.
Als Museumswagen ist Wagen 5274 erhalten geblieben, dieser stand auch Pate für das Modell.
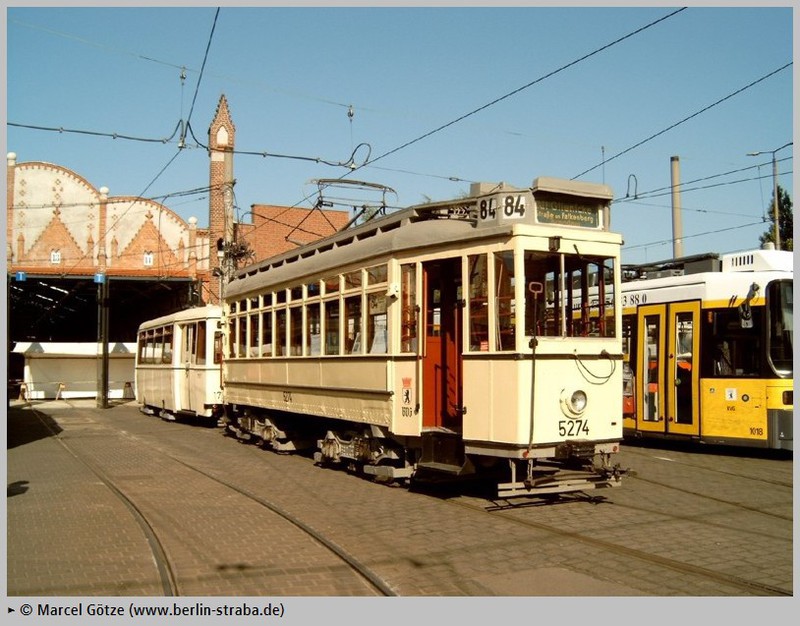
Das Modell:
Als Voraussetzung für eine Modellumsetzung haben wir Zeichnungen gesucht, die von Familie Kubig auch freundlicherweise zur Verfügung gestellt wurden. Diese stammen aber von der Ursprungsversion. Deshalb musste -zumindest für die Plattformmaße- das Original vermessen werden, damit Bodo-Lutz Schmidt an die Erstellung der 3D-Zeichnung gehen konnte.
Nach Fertigstellung und einer ersten Kontrolle wurden dann die Dateien zum Druckdienstleister versendet. Der Werdegang des Modells beim Druckdienstleister wird hier von IBG einmal genauer beschrieben:
Allgemeines:
Stereolithographie (kurz STL) ist das älteste und bekannteste der generativen Fertigungsmethoden. Dabei wird Resin, mittels Photopolymerisation (UV-Strahlung) in die feste Phase überführt.
Neben einer Reihe von Vorteilen bietet die Stereolithographie auch Nachteile:
Wenn ein Bauteil fertiggestellt ist folgt eine Behandlung, dass sogenannte post-processing. Hierbei wird das Bauteil gereinigt und ggf. von Stützmaterial befreit. Es folgt ein nachträglicher Prozess im UV-Ofen, welcher die Endfestigkeit des Materials Gewährleistet.
Optional können Bauteile eine zusätzliche Oberflächenbehandlung erhalten. Vom Schleifen über das Polieren bis hin zum Lackieren.
3D-Daten aufbereiten
Die 3D-Daten des Kunden müssen zunächst aufbereitet werden. In wenige Ausnahmefällen sind dabei auch Reparaturen am 3D-Modell erforderlich. Diese Phase ist, neben dem „post-processing“ am Ende der Prozesskette, wesentlich entscheidend für finale Qualität des fertigen Druckteils. Bauteileile werden unter den Kriterien …
1. Qualität und Details
2. Machbarkeit
3. Kosten respektive Druckzeit
… im virtuellen 3D-Drucker Bauraum platziert.

Die Stützstellen werden in über 90% der Fälle von Hand gesetzt was, je nach Bauteilkomplexität, mit sehr viel Aufwand verbunden ist.
Das manuelle Platzieren ist deshalb erforderlich, weil kein Software-Algorithmus in der Lage ist, die Entscheidungen und Einschätzungen zur Platzierung der Stützstellen unter Berücksichtigung der Kundenanforderung zu treffen. In wenigen Ausnahmefällen lassen sich Bauteile auch ohne Stützen direkt auf der Plattform drucken. Die 3D-Daten werden kompiliert und an den Drucker gesendet.
Dieser baut nun Schicht für Schicht die Teile auf.
Drucker
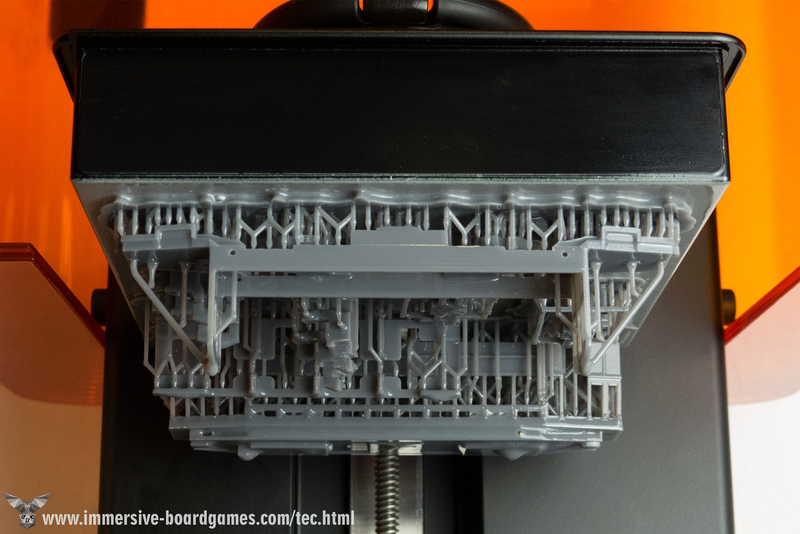
Nach dem Druckvorgang hängen die Bauteile überkopf, sodass überschüssiges flüssiges Resin in den Tank ablaufen kann.
Entfernen von Druckplatte
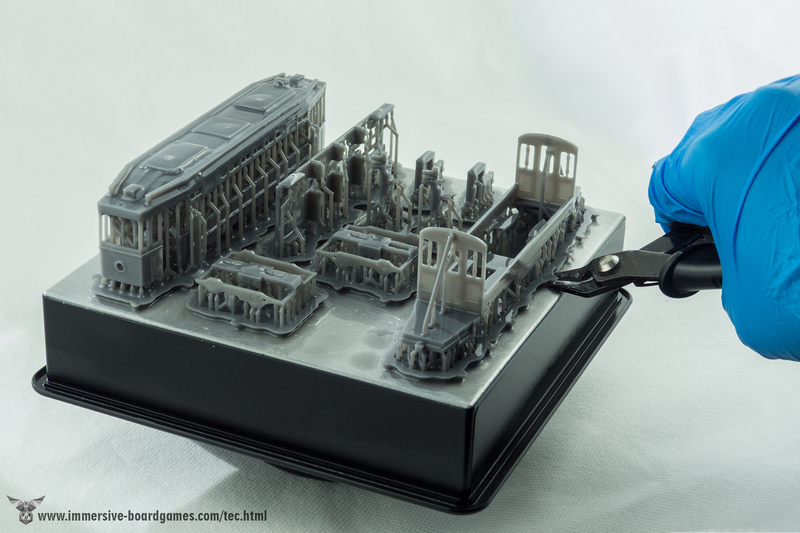
Nach der Entnahme der Bauplattform aus dem 3D-Drucker müssen die Bauteile von der Plattform abgehoben werden.
Waschen im Isobad - Trocknen

An den Bauteilen haftet immer noch flüssiges Resin, weshalb diese ein mehrstufiges Isopropanol-Bad durchlaufen. Anschließend müssen die Bauteile an Luft trocknen.

UV-Behandlung
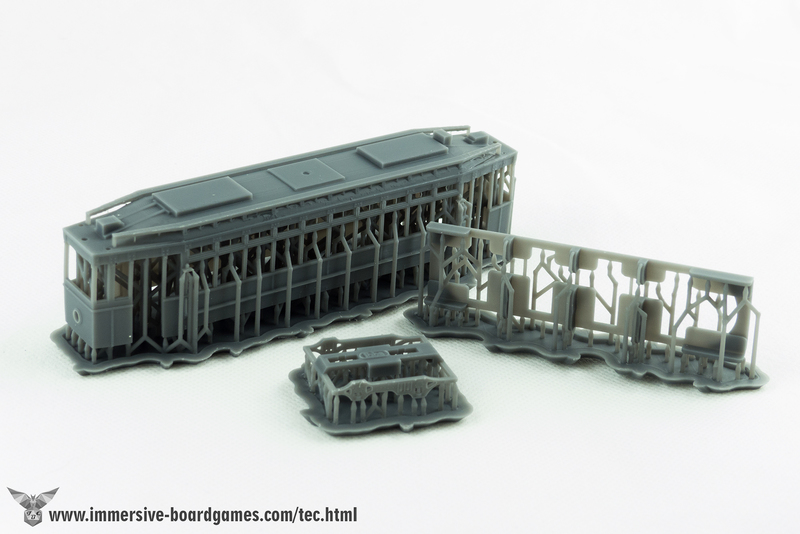
Nach der Trocknung gehen die Bauteile in die UV-Kammer, wo sie unter Einfluss von Temperatur (ca. 60° C) und UV-Licht, mit definierter Wellenlänge und Intensität, aushärten um Ihre Endfestigkeit zu erreichen.
Schleifen
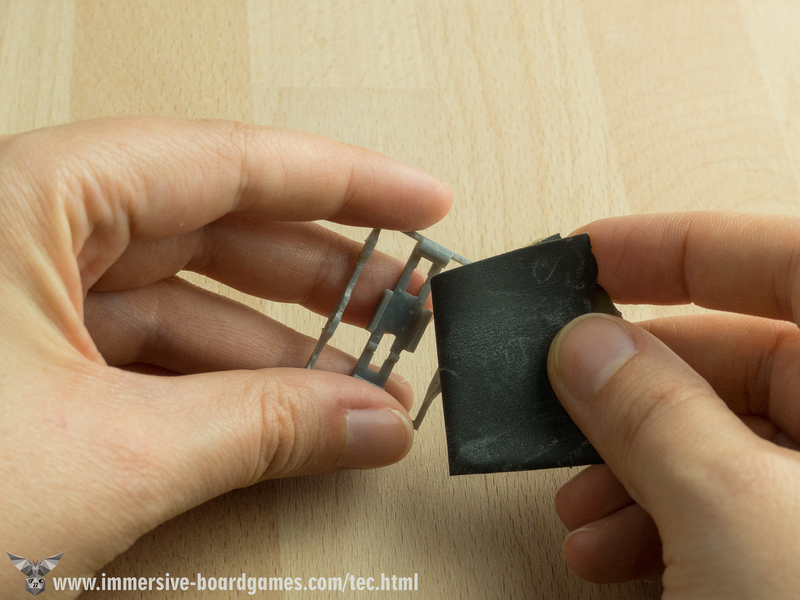
Zu guter Letzt kommt die Nachbearbeitung das sogenannte „post-processing“. Dazu gehört stets das Entfernen des Stützmaterials und das Schleifen der noch sichtbaren Ansatzpunkte, wo Stützen und Bauteil einst zusammen trafen. Diese Arbeitsgänge am Ende der Wertschöpfungskette sind besonders kritisch, da hier jedes Bauteil eine manuelle Behandlung erfährt und Ausschuss mit hohen Kosten und Aufwand verbunden ist – eben echte Handarbeit.
Zusammenbau nach Lieferung durch Druckdienstleister:
Die Teile für die Prototypen kamen gut verpackt an. Somit werden Transportschäden weitgehend ausgeschlossen. Beschädigt gelieferte Teile bitte sofort reklamieren, sie werden kostenlos ersetzt.
Vor dem Lackieren sind kaum Nacharbeiten erforderlich.

Die Teile wurden mit OBI Spritzspachtel grundiert und anschließend mit Sprühfarbe (Autolack) gespritzt. Besonders bei den Drehgestellrahmen besteht Bruchgefahr wegen der dünnen Streben.
Sie sollten wie rohe Eier behandelt werden.
Die schwarzen Zierstreifen wurden mit einem lichtechten Stift aufgebracht und später mit farblosem Lack gesichert.

Beim Zusammenbau haben wir dann sämtliche Hinweise auf zu verändernde Teile gesammelt, um diese dann in der Konstruktion für die "Nullserie" berücksichtigen zu können.
Es wurde dabei ein Standmodell und ein motorisiertes Modell gebaut, um beide Varianten in der Passgenauigkeit zu testen. Beim Standmodell ist die Inneneinrichtung komplett vorhanden, beim motorisierten Modell ist dem Platz für Motor und Getriebe Rechnung getragen, die Sitze wurden daher etwas in der Höhe reduziert und auf einer aufzulegenden Sitzplatte zusammengefasst.
Die Drehgestelle des Standmodells sind nicht angetrieben, aber rollfähig. Sie können nachträglich nicht gegen angetriebene Drehgestelle getauscht werden.
Nach Abschluss der Dekoration und Lackierung konnte die Verglasung mit den gefrästen Fenstern beginnen.
Hierbei hat sich herausgestellt, dass die Fenster mit 1 mm Stärke (davon 0,5 mm als Bund) zu dünn wirkten und auch nicht ausreichend stabil eingesetzt werden konnten.
Für die Serienmodelle wurden daher dann 1/1,5 mm starke Fenster vorgesehen.
Für den Antrieb wurden Bauteile von Halling verwendet. Dafür waren mehrere Versuche nötig. Der Motor treibt über Silikonschläuche beide äußeren Achsen an, also wie beim Original.

Um einen Beiwagen ziehen zu können, muss der Wagen mit ausreichend Gewicht versehen werden, z.B. unter dem Dach. 2 Beiwagen können nur gezogen werden, wenn ein Treibradsatz mit Haftreifen versehen wird. Der Antrieb ist nur für H0 vorgesehen, nicht in H0m verwendbar, da die Aufnahme für die Drehgestelle zu viel Raum einnimmt.
Mindestradien bis 20 cm werden problemlos durchfahren.
Zum Abschluss muss der Wagen dann noch mit Fangkorb und Tastgitter, sowie Kupplungen versehen werden. Diese sind nicht Bestandteil des Teilesatzes, wir haben hier die Zusatzteile vom Halling KSW verwendet.
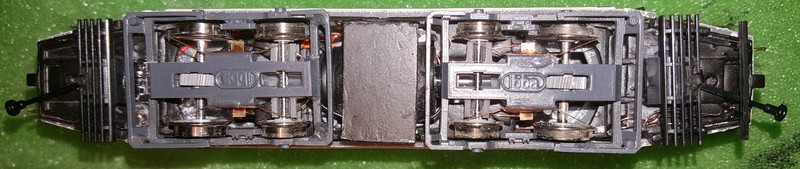
Die Griffstangen wurden aus 0,5 mm Draht gebogen.
Nach den Erfahrungen mit den Prototypen wurde dann ein Modell mit einigen Veränderungen gebaut - (Nullserie). Dieses wurde auch mit Beleuchtung versehen. Hier kommt die Möglichkeit des Druckes transparenter Teile für die Liniennummern- und Zielkästen zur Anwendung. Dafür wurden von hinten in den transparenten Zielkasten 2 kurze Löcher gebohrt, kleine SMD-LEDs eingesetzt und verleimt.
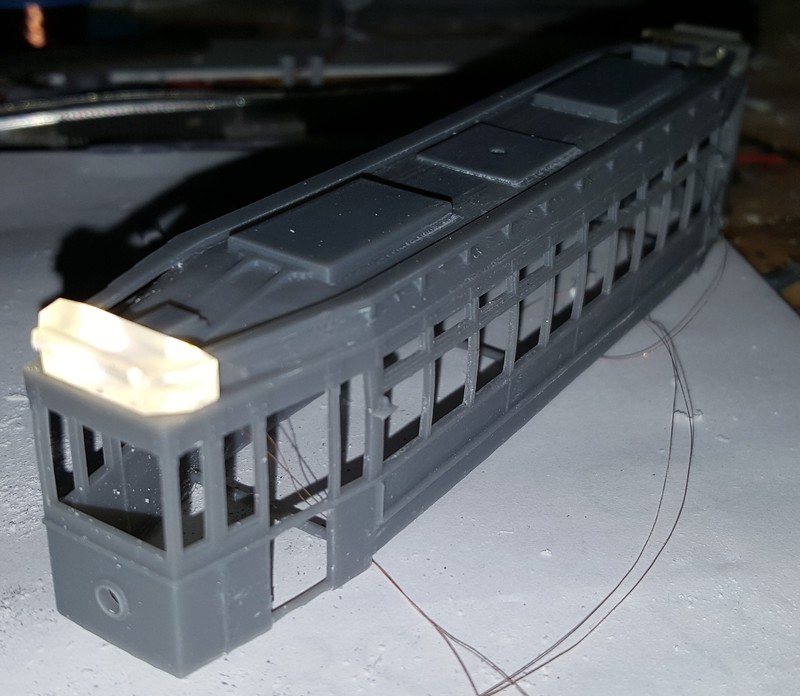
Der Kasten sollte - wenn er beleuchtet werden soll - vor dem Aufkleben auf das Dach vorn abgeklebt werden und die nicht leuchtenden Flächen schwarz lackiert werden.
Insgesamt muss gesagt werden, dass der Zusammenbau bis zum fertigen Modell nur für erfahrene Bastler geeignet ist.
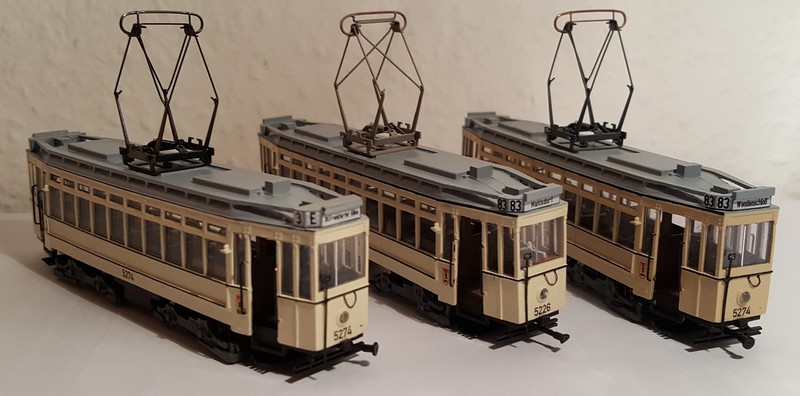
Gruppenbild aller 3 Musterfahrzeuge (links Nullserienfahrzeug, mittig Prototyp ohne Antrieb, rechts mit Antrieb
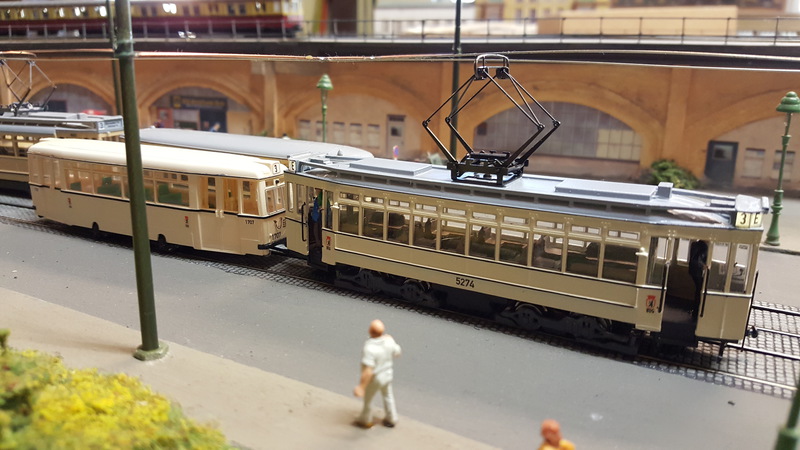
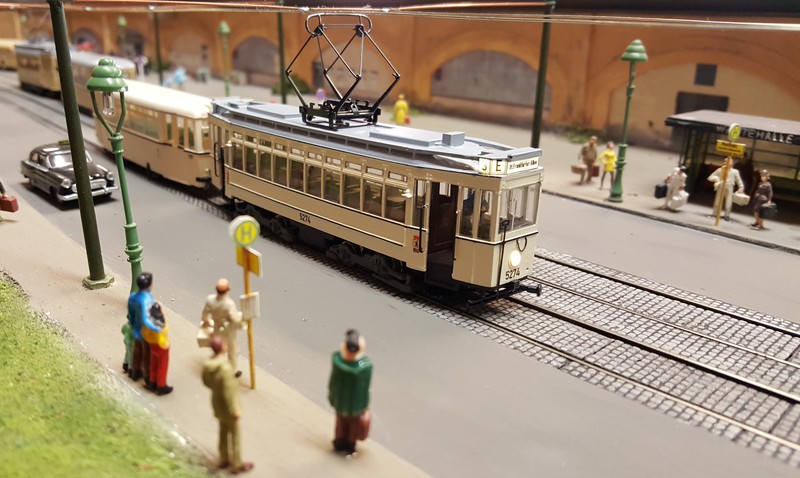
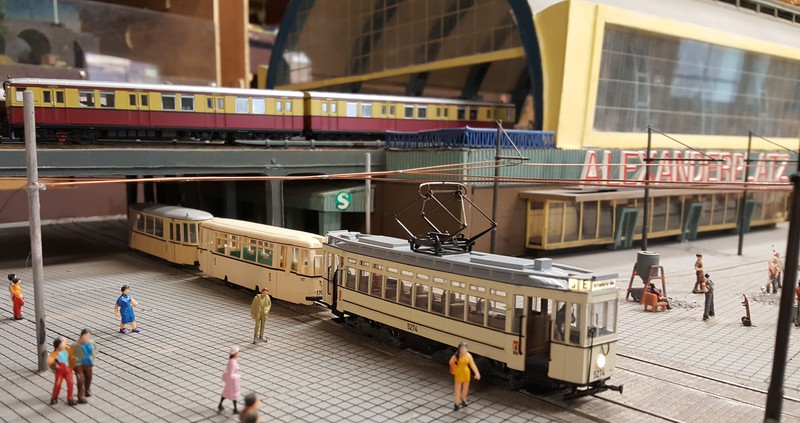
Das fertige Nullserienmodell im Testeinsatz auf der Berliner S-Bahn-Anlage des Vereins Weinbergsweg.
Die Teilesätze sind ab sofort unter service@immersive-boardgames.com bestellbar.
Hierbei gelten folgende Artikelnummern und Preise:

zusätzlich sind noch folgende Bauteile nötig:
Fenstersatz gefräst - erhältlich auf Anfrage bei Bodo-Lutz-Schmidt (bolusch@freenet.de)
Wagennummern und Zielbeschriftung erhältlich auf Anfrage bei Jan Ruppert (jan.ruppert@freenet.de)
Teile von Halling (http://www.halling.at):
2 H0-Achsen 9mm mit Zahnrad (ggfs. ein Radsatz mit Haftreifen)
2 H0-Achsen 7mm ohne Zahnrad
2 Schnecken + Welle wie Wiener E
4 Federblechstreifen Stromabnahme für Lauffahrwerk Variobahn
1 Motor ohne Schwungmasse wie für Wiener E
1 Satz Zurüstteile KSW
zusätzlich werden benötigt: Silikonschlauch (ebay), Innendurchmesser 1mm
und Walzblei, um das Wagengewicht zu erhöhen.
Dünner Messingdraht <0,5 mm für Griffstangen und Bremskabel, Weichensteller
Alles zusammengerechnet betragen die Materialkosten etwa 200 Euro pro Wagen.
Bitte beachten! Es werden lediglich Teilesätze angeboten. Fertigmodelle sind aus Zeit- und Kapazitätsgründen nicht möglich.
An dieser Stelle einen recht herzlichen Dank an Bodo-Lutz-Schmidt für die Erstellung der Zeichnungen, er hat ja den Hauptanteil bei der Umsetzung.
Ebenso geht der Dank an Herrn Arlt von IBG für die Umsetzung der Drucke.